Aerodynamic design
AG Consultant has a great experience in the aerodynamic design methods of industrial fans.
Historically fan designers have used experimental design techniques based on model testing, applying variants of the model to gradually improve fan performance and efficiency.
This method obviously required a great deal of time to develop geometric model variants.
Now the development of computers and numerical methods in Computerized Fluid Dynamics (CFD) offers the possibility of developing variants on a virtual fan described numerically to improve the design, before conducting air performance testing and validation in a laboratory.
This has been the case for the design of the two large contra-rotation impellers of the wind-tunnel S1 of ONERA at Modane-Avrieux (France).
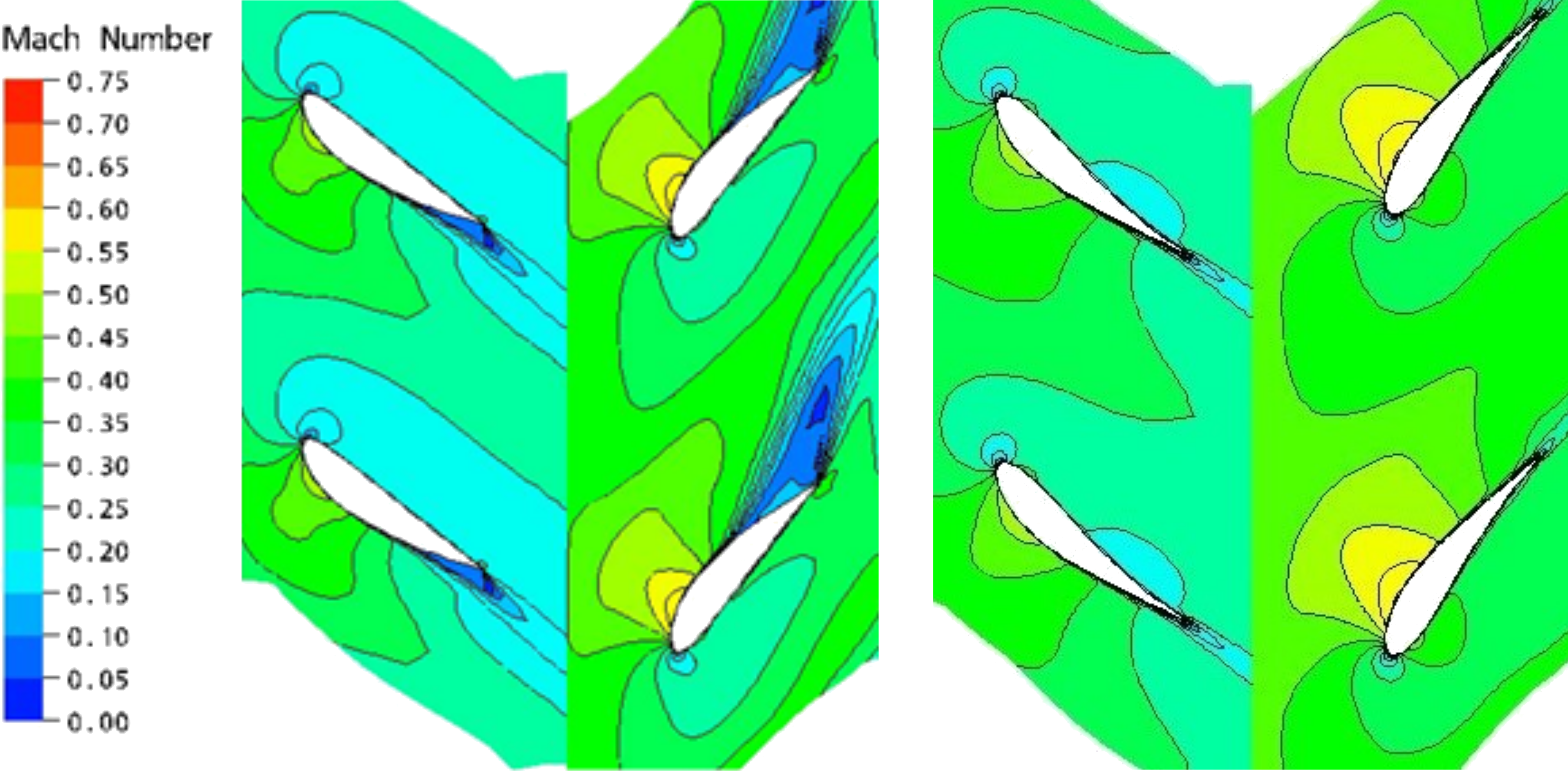
Mach number on a given meridian section at nominal flow comparison between old design (left) and new design (right)
Source: courtesy of ONERA and Howden Solyvent-Ventec
The pictures above illustrate the design improvements at the nominal flow. At a given section, the old design on the left exhibits a severe flow separation at the trailing edge of the second impeller while the new design with the blade profile modification shows that this flow separation disappeared in the same operating conditions.
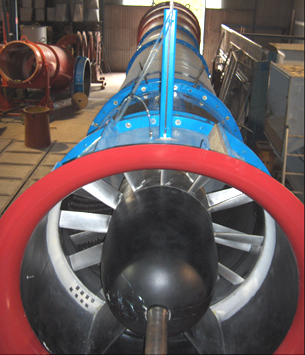
Fan performance test in laboratory with a model at reduced scale 1:12.5
Source: courtesy of ONERA and Howden Solyvent-Ventec
Following the numerical study, a fan performance test was performed with various operating conditions. Due to the large size of the wind-tunnel fan diameter: 15 m [49.2 feet], a significantly reduced scale was applied with a model diameter of 1.2 m [scale 1:12.5]. Nevertheless the operating speed was relatively high for the model in order to get during testing Mach and Reynolds numbers at acceptable levels compared to the actual fan, and make reasonable the performance estimation. A significant improvement in fan efficiency on a wide flow range was confirmed for the new design.